Maintenance controller Xavier “Cisco” Cisneros (’97, ’06) could spend his 12-hour shift monitoring 30 to 40 flights from Hawaiian Airlines headquarters in Honolulu. He is on call, four days on and four days off, to advise flight crews on how to deal with anything from first-class seats that won’t recline, leaking coffeemakers or smoke detectors that won’t turn off after someone has been vaping in the lavatory.
There was one emergency in September 2021 that Cisneros recounts here for us in his own words.
“Hey, Cisco … we left Korea.”
I knew the pilot on the satellite phone well. I also knew that he was about five hours into an 11-hour flight back to Honolulu.
The A330-200 captain wasn’t calling Maintenance Control to chat. He had a problem for me to troubleshoot. I just had no idea how big a problem it was.
“My left engine is showing no oil pressure. It’s super low. It’s still running. How is that possible?”
His plane can take off and land safely with one engine, according to ETOPS — Extended-range Twin-engine Operational Performance Standards. However, it’s not safe to fly with one engine because if any little thing happens to the functioning engine, you’ve got no more lift.
“We both hoped it was an indication glitch, but we couldn’t proceed on that assumption. An indication would fluctuate up and down, and that’s not what we were seeing.”
Xavier Cisneros (’97, ’06)
I asked, “Do you have secondary indications? High temperatures? Fuel problems?”
“Engine is normal … but we are supposed to have 17 quarts, and I’m at 13. The other side is at 17.”
We both hoped it was an indication glitch, but we couldn’t proceed on that assumption. An indication would fluctuate up and down, and that’s not what we were seeing. I called in an engineer to view the portals to spot engine abnormalities. He didn’t but pointed out that a few days earlier, maintenance was done near the oil tank area that may have disrupted the system and caused a leak.
The situation turned dire. The pilot reported, “I’m down to 10. The oil indication keeps dropping but the engine seems to be running normally.”
If the oil level drops to six quarts, the engine must be shut down before it is seriously damaged, to the tune of several million dollars. We had to get with a dispatcher to identify the nearest suitable airport.
I advised the pilot that the nearest option was a small landing strip on Midway Atoll, about 34 minutes out — and at the rate he was losing oil, getting there would put him right around 6 quarts.
The pilot, dispatcher and I agreed it was safest to land. Our pilot’s decision to declare an emergency initiated a new round of problem-solving and support. Midway Atoll is not an ideal landing spot for an A330-200 airplane. Most of the island is home to an old U.S. Navy base now functioning as a National Oceanic and Atmospheric Administration tide/tsunami monitoring station. Henderson Field is a small public airport with one runway and no control tower adjacent to a large bird sanctuary.
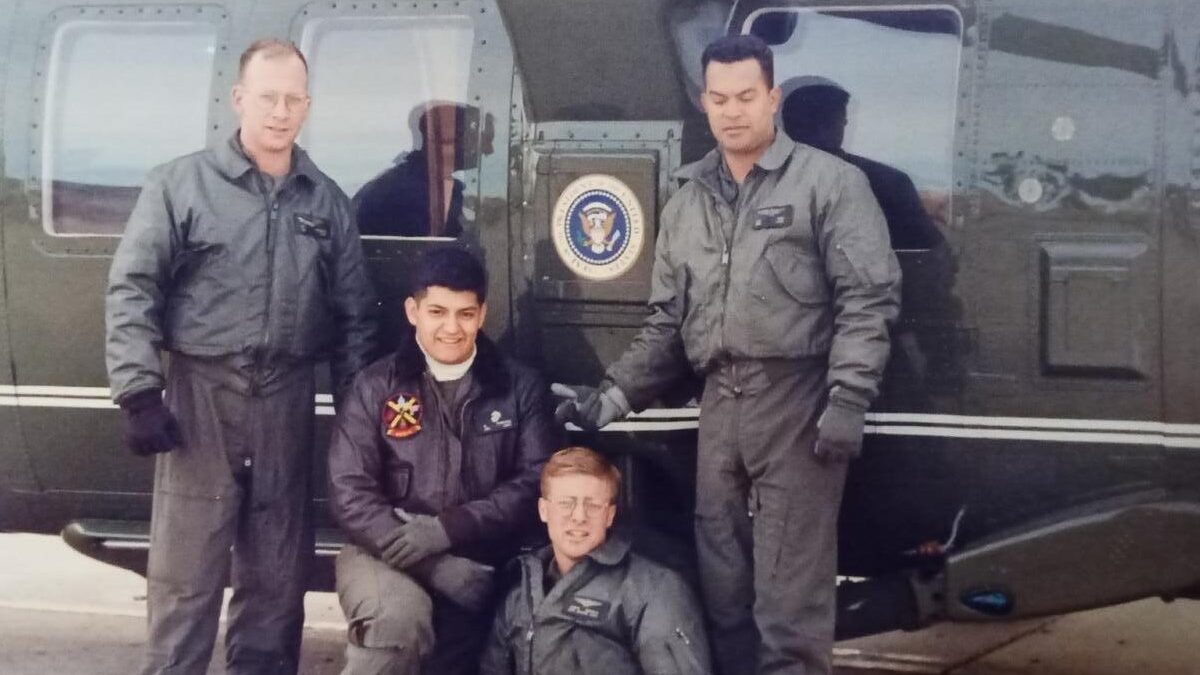
The pilot made a safe landing but deplaning his passengers was the next challenge. There was no jet bridge or staircase to reach the huge plane. Activating emergency slides was an option, but a local carpenter quickly built emergency stairs to bridge a six-foot gap that would otherwise trap people inside the airplane.
On the ground, the pilot was able to inspect the engine. What he saw confirmed that we made the right decision.
“The whole side of the engine cowl is full of oil.” Pressing on to Honolulu could have been catastrophic for the passengers and crew aboard.
Hawaiian Airlines sent a rescue plane with crew members and mechanics without knowing the root cause of the problem. There were no mechanics on the island who could even open up the engine cowling. Back at headquarters, I was studying computer graphics of the engine and running through a list of potential issues: oil cap, packing, O-ring on the oil cap, line. We needed to figure out which parts and tools to pack to perform the necessary repairs. And of course, we were going to need oil.
One of the tank oil lines that was suspect was not in supply. We had a spare engine, and I asked the mechanics to take the oil line from it. They were understandably resistant. It was labor-intensive and the engine mounts in the way made it challenging to extract the hard-to-reach line. I had to make a decision based on little more than an educated guess. I insisted, “We are not releasing a rescue plane until I have that line.” It took them more than 90 minutes to deliver it.
At Midway, we confirmed that the tank oil line was the problem. (Maybe I wouldn’t be telling this story if it had turned out to be some unrelated issue.) The spare engine line fixed the issue. The rescue aircraft picked the passengers and continued to Honolulu after a delay of approximately nine hours.
Flight HA460 was eventful for everyone involved, but collaboration, good communication and decisive action kept everyone safe.
Xavier Cisneros earned his bachelor’s in Professional Aeronautics from Embry-Riddle Worldwide in 1997 and returned in 2006 to earn his Master of Business Administration in Aviation. He is a maintenance controller at Hawaiian Airlines.